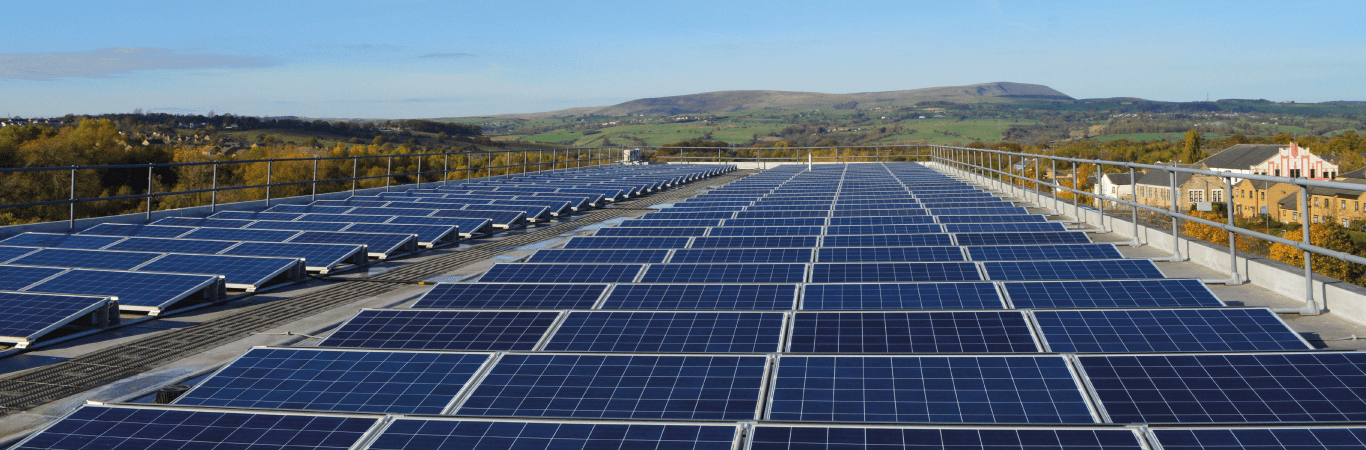
May’s energy saving tip
Production Equipment
Process and production equipment is vital to operations. Whether you’re using motors as part of your manufacturing process, compressed air in your garage of refrigeration equipment as part of a retail business, energy use from production equipment is everywhere. It’s important to understand where you’re using energy, and smart meters can help you do this. Older, poorly maintained and inefficient equipment is one of the biggest culprits for energy wastage, so this section covers some simple steps to help you minimise it.
Motors and drives
You know that motors are integral to your process, and the longer they run and the hotter they get, the more it costs you. A few simple zero-cost steps can help reduce both costs and the risk of breakdowns:
Make sure
Motors are switched off when not in use, i.e. during breaks and at lunch
All machines are turned off at the end of the day – don’t get forget fans, pumps and conveyors
Switches are labelled and staff are trained in the correct procedures for operating machinery so they know what they can turn off
You establish the optimum settings for equipment, such as the speed of fans, and communicate this to staff
Motors are kept clean – a dirty motor will get much hotter than a clean one and is more likely to fail
Compressed air
Compressed air is essential to the operation of many processes and is often considered as the ‘fourth utility’. But it is very expensive when looking at it cost per unit of energy delivered, especially when it leaks. Not only does a leaky compressor create a noisy working environment, a single 3mm hole can cost you nearly £700 a year. The following simple no or low-cost changes can reduce the cost to you and improve safety:
Make sure
Compressed air is turned off when you don’t need it. An idling compressor still uses between 20-70% of its full load power.
Pressure is set at the lowest possible level for each application. Reducing air pressure by just 10% can lead to 5% energy savings
You listen for and fix compressed air leaks
Unused runs of pipework are isolated to help eliminate leaks
Condensate traps are checked to ensure none are left open
There’s adequate ventilation around the compressor – this will improve its efficiency
Refrigeration
You know that the more heat that gets into refrigerated and cooled space, the more energy it will take to cool it. For refrigerators to work efficiently, air needs to circulate freely both inside and out – if not, running costs can increase by up to 10% and products won’t be sufficiently cooled. The following simple measures will ensure heat gains are kept to a minimum and the system operates efficiently:
Make sure
Doors are kept closed to keep warm air out
Lights inside cooled spaces are switched off when not needed
Areas are only cooled to the temperature you need. Every 1°C increase reduces energy use by 2%
Refrigeration units aren’t overfilled so that cooling air can circulate
Freezers are defrosted regularly to avoid ice build-up
Condensers (external) are regularly cleaned to help prolong life, hill faster and therefore reduce costs, and evaporators (internal) are regularly defrosted
There is space around refrigeration unit vents to allow air to be drawn in and expelled more efficiently
Fridges and vending machines containing non- perishable items are switched off when they are not in use, like at the weekend
Up to 20% of energy use in refrigeration can be cut with little or no investment
Energy Technology
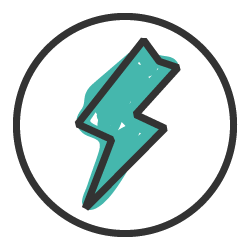
Powering your present. Preserving your future.
Call us on 01282 421 489
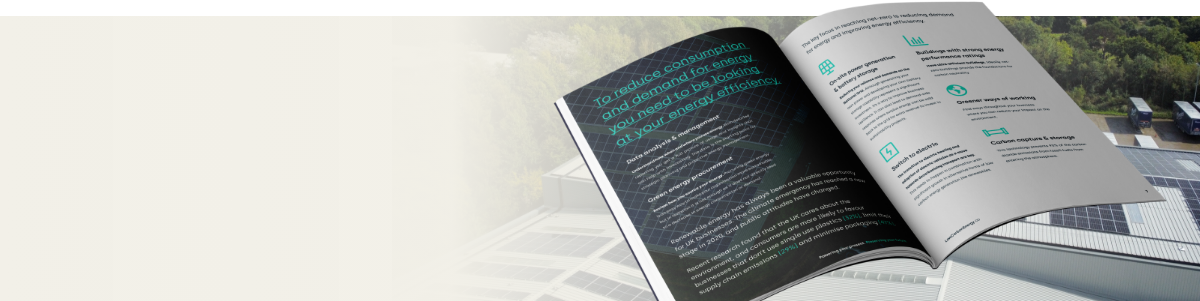
strategy be a priority?